NEW AND IMPROVED Farmhouse Table Details
Thanks for stopping by our blog. We hope this blog post is a great resource for you. Feel free to browse around for other ideas/inspiration. If you like what you see, we’d love to hear from our readers….drop us a comment at the end. Also, we’re fairly new to the whole blogging world and would love for you to join us in this adventure by following…our time is limited but we try to update it often. Thanks, Tommy and Ellie.
It wasn’t too long ago when I took on my first big building project….the infamous Farmhouse Table. I had little clue of what I was doing but I moved forward anyways.
Since then, I’ve built similar tables for friends, family, and strangers. Each time that I’ve built the table, I’ve learned one or more tricks on either simplifying the process or making a better quality product. I look back at the original post and almost cringe with embarrassment about certain aspects of how I used to build the table…..that’s why I decided to document my latest table with more pictures, more details, more measurements, and hopefully more resources to better equip others to make a similar table.
I have to start by giving all the credit to the Ana-White website and Restoration Hardware.
These instructions are to create a table with the dimensions 96″x41″. I put together a cut list and shopping list pdf for both a 96″x45″ table, matching bench, and extensions AND a 72″x41″ table, matching bench, and extensions ~~~~>
I purchased all the wood from a local mill. I bought all #2 kiln-dried pine. Here’s what I purchased to build the table, the bench, and the extensions;
- 2: 2×12
- 2: 2×10
- 5: 2×8
- 10: 2×4
- 3: 4×4
- Planks: 2: 2×10″s @ 81″
- Planks: 2: 2×12″s @ 81″
- Breadboards: 2: 2×8″s @ 41″
- Legs: 4: 4×4″s @ 28.5″
- 4×4 Stretcher: 2: 4×4″s @ 38.25″
- 2×4 Bottom Stretcher: 1: 2×4″ @ 88.25″
- Side Aprons: 2: 2×4″s @ 81″
- End Aprons: 2: 2×4″s @ 31″
- Inside End Aprons: 2: 2×4″s @ 34″
- Supports: 3: 2×4″s @ 34″
- 2.5″ Kreg screws
- Wood glue
- Lots of 100 grit sandpaper
- Router with 1/2″ round bit
- Table Saw
- Circular Saw
- Lots of clamps
- Minwax Special Walnut
- Minwax Clear Gloss Poly
- Briwax Light Brown (you’ll probably need two cans)
Here’s some basic building plans that I whipped together using Keynote to help serve as a visual;
I decided to start this table by beginning with the tabletop. I take my 2×12″s and my 2×10″s and lay them on my concrete floor. I then mess around with different possible arrangements and look for any irregularities in the edges and fitment of boards next to one another as well as determining what will serve as the topside of the boards. For this table, I went with a 2×12, 2×10, 2×12, 2×10, pattern. The way the seams lined up on these planks were staggered so I marked off one end and cut them square (I left the opposite end untouched).
The end that was cut would become the end that I would line up flush during assembly. I made a mark 81″ from the edge so that I know where to distress/sand. To distress the wood, I take out a few items found around my garage and randomly hit them against the wood to create small indentations. I used to think that I wanted it distressed a whole lot but have come to find that I prefer for it to be subtly distressed. I have a couple of staple marks that I like to create one of which being a knot in the middle of the table that appears old/worn/weathered. To accomplish this I take my chisel and hammer and chisel away some at the knot.
After it’s distressed I make my marks for pocket holes. One of our readers recently made an amazing table and used dowels so I decided to give that a try for the first time ever on this table and I loved it. I purchased the same jig that he used found here. If you don’t own a jig or want to buy one…..no worries, just skip over the dowels and use pocket holes (that’s how I made all my other tables). To create pocket holes you’ll need a Kreg Jig…..hands down one of the best tools you can own. I created a little picture to demonstrate how I drill my holes. Here’s the measurements of each hole (Measurements starting from the flush end);
Pocket Holes (alternating every other from board to board)
- 4″
- 16″
- 28″
- 42″
- 52″
- 64″
- 77″
- 2.5″
- 21.5″
- 40.5″
- 59.5″
- 78.5″
Once the holes were drilled, I sand each board down individually. I use a palm sander with 100 grit sandpaper. I sand down the spots that I distressed, the knots, the edges, and pencil marks.
Time for assembly. I use some wood glue for the dowels, place them in, and begin to clamp the first two planks into one another. I use an excessive amount of clamps for this part (it may be overkill but my preference is to have nice tight fitting seams).
Once all four planks are screwed together, I test fit the breadboards onto the flush end and find the best fitting board. I take the other board to the other end. I mark the planks at 81″ and clamp down the breadboard to the planks to create a straight line for me to cut along. I then unclamp the breadboard and give it a test fit.
I created the jpeg below to show you how I drilled the pocket holes and dowel holes for the breadboards. To drill the holes on the planks, I clamp down one of the Kreg Jig accessories approximately 1.5″ from the edge.
Pocket Holes
- 2″
- 9″
- 15″
- 22.5″
- 30″
- 33.5″
- 39″
- 4″
- 13″
- 18.5″
- 24″
- 28.5″
- 37″
I use wood glue for the dowels as well as the seam for the breadboards to the planks. I use a series of clamps to try and ensure that it fits tight and level. Once those are attached, I use my router to round off all the edges (top and bottom) and give it another good sanding. I then move the tabletop off to the side.
The hard parts over and you can give it all a good test fit. If you make your cuts with precision/accuracy you should have fairly tight fitting pieces.
I use the same tools as I used on the tabletop and distress on the exposed faces of the boards that will form the base.
Once distressed, I drill my pocket holes using the Kreg Jig. For the top holes I clamp down the Kreg Jig accessory.
- Top edge of each side
- Bottom inside edge of each side
- 4 holes going towards the top; 4″, 24″, 57″, 77″
For the end aprons (2x4x31);
- Top edge of each side
- Bottom inside edge of each side
- 4 holes going towards the top; 3″, 11″, 20″, 28″
- Top inside edge of each side
- Bottom inside edge of each side
- 4 holes going towards the top; 4.5″, 12.5″, 21.5″, 29.5″
- Top inside edge of each side
- Bottom inside edge of each side
I then clamp in place the inside end apron. I don’t have holes drilled for these screws, I just drive them straight in avoiding the pocket holes that I drilled (those will be to attach to the side aprons). The 4×4″ stretcher is clamped and screwed into place using the countersink holes.
I then repeat the process for the other set of legs.
I then add the supports into place. The first support goes 20″ from the edge of the 4×4″ or approximately 21.75″ on-center. The second support goes in approximately 44″ on-center. And the last one goes in 20″ from the edge of the other 4×4″s edge. (I apologize for the crumby pictures….not sure what happened)
I then center the bottom stretcher and clamp it down. I turn the table onto it’s side so that I can drill the screws in from underneath.
After the table’s assembled I cut out the notches to allow for the extensions. To do this, I find my center on the end apron and inside end apron. I then measure off 10″ from center in both directions and use a square to make my mark across both 2×4″s. I then make an additional mark 11.5″ in both directions from the center. I clamp down a scrap piece of wood to give me a flat surface to run my circular saw along. With that board in place, I adjust my saw blade to an exact depth of 1.5″. I make my first cut, my last cut, then several cuts in between. I then chisel out the slivers and use the circular saw to sand down the roughness.
I almost forgot. I like to drill one more pocket hole through the 4×4″ in between the end apron and the inside end apron. I like the idea of the strength of the 4×4″ and I also like to get a bunch of screws that will go straight into the breadboard. The table is extremely heavy and I envision someone trying to pick up/move the table by grabbing the breadboard and seeing it snap off….so better safe than sorry. (you’ll notice I did this after I stained the table….oops);
Table construction done! Time for the finish.
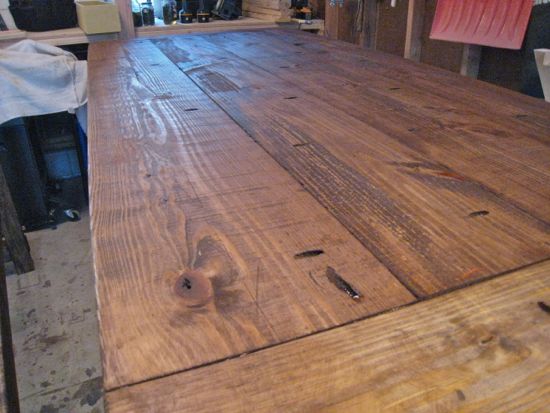
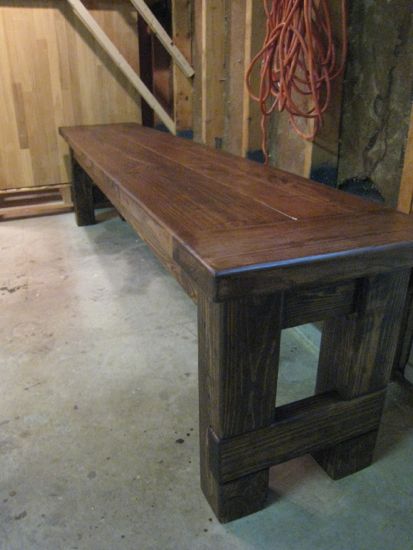
Now it’s just time to attach the tabletop to the base. I found the easiest way to do this is to use the extensions as a way of helping me align the center of the tabletop. I place the extensions in and use my hand to align it all. I then just measure out a 4″ overhang on both ends. Once it’s in place, I clamp it all down, climb under the table, and screw it into place using all the pocket holes created in the aprons and a few screws through the supports.
There you have it…..the new and revised details of how to build your own Farmhouse Table. It’s crazy detailed and I hope that it all makes sense. Let me know if you have any questions/feedback…….I’d love to help.
Trackbacks
There are no trackbacks on this entry.
Comments
There are no comments on this entry.